To create value for customers, to be proud
of customers' continuous satisfaction
AISI A8 Tool Steel
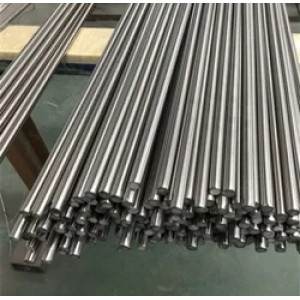


Categories | Tool Steel Bars |
---|---|
Brand | fushun |
Model | A8 |
Process | hot rolled or hot forged |
Delivery Condtion | annealed |
Surface Condition | smooth, bright |
FOB port | Shanghai |
Terms of Payment | L/C, T/T |
Update Time | Apr 29,2024 |
AISI A8 Tool Steel
Introduction
A8 is an air-hardening cold work tool steel. It exhibits good wearing qualities with excellent toughness characteristics. It is well suited for many metals working dies and punches, which operate in the hardness of Rockwell C 55-60.
Applications
Punches, drift pins, pneumatic tools, chuck jaws, hammers, hot rolls, and hot and cold shear knives.
Quality Standard
ASTM A681 – 08 Standard Specification for Tool Steels Alloy.
Chemical Composition(%)
C | Si | Mn | P | S | Cr | Mo |
0.50-0.60 | 0.10-0.70 | 1.80-2.50 | 0.030 max | 0.030 max | 0.90-1.40 | 0.90-1.40 |
Heat Treatment
Preheating: Heat at a rate not exceeding 400°F per hour to 1400-1450°F and equalize.
Austenitizing: Heat slowly from the preheat. Furnace or Salt: 1825-1850°F. Soak for 30 minutes for the first inch of thickness, plus 15 minutes for each additional inch.
Annealing: Annealing must be performed after hot working and before rehardening.
Heat at a rate not exceeding 400°F per hour to 1550°F, and hold at temperature for 1 hour per inch of maximum thickness; 2 hours minimum. Then cool slowly with the furnace at a rate not exceeding 50°F per hour to 1000°F. Continue cooling to ambient temperature in the furnace or in air. The resultant hardness should be a maximum of 241 HBW.
Hardening: Air, pressurized gas, or interrupted oil to 150-125°F.
Note: Sizes over 5 inches in cross section may not achieve full hardness by cooling in still air. It is usually necessary to increase the quench cooling rate between 1400 to 900°F by using an air blast, pressurized gas, or an interrupted oil quench. For the oil quench, quench until black, about 900°F, then cool in still air to 150-125°F.
Tempering: Temper immediately after quenching. Hold temperature for 1 hour per inch of thickness, 2 hours minimum, then air cool to ambient temperature. The typical tempering range is 300 to 600°F. Double tempering is recommended for tempering temperatures of 900°F and higher.To minimize internal stresses in cross sections greater than 6 inches and to improve stability in tools that will be EDM’d after heat treatment, a soaking time of 4 to 6 hours at the tempering temperature is strongly recommended.
Mill′s test certificate
EN 10204/3.1 with all relevant data reg. chem. composition, mech. properties and results of testing.
- Tel
- *Title
- *Content
- Name:
- Florence Tang
- Tel:
86-731-89903933
- Email:
- info@fushunsteeltube.com
- Address:
- ADD: No. 812-813, Floor 8, Building C2, Yongsheng Commercial Plaza, 222 Labor East Road, Yuhua District, Changsha City, Hunan, China.
sign up for the latest catalogue, new design and promotion